London School with Superstructure Issues & Bowing Walls
This primary school in Southwark, London, had significant visible bowing to the second-floor right side flank wall, putting the structure at risk of collapse. Progressive movement was impacting the entire building and required a plan to reinforce and restrain all the brickwork. Previous repairs had failed to halt the movement of the structure.
According to estimates, to repair the defects using traditional building methods the school would need to close for 6 months. AWT completed their work in just over 2 weeks during the school summer holiday. AWT’s work was also significantly cheaper, accounting for less than 25% of the original projected cost.
AWT worked with the Education Service and the consulting structural engineers to design a permanent, cost-effective structural repair that would minimise disruption to the school’s staff and pupils.
The Structural Problem
The building was a Victorian/Edwardian period property that had been extended and converted into a school. There was significant visible bowging to the front section of the second-floor right side flank wall. There was also bulging brickwork between the rear third floor windows.
These structural defects were severe – nearing the tipping point. Without urgent action, the structure would collapse. The rest of the property was also suffering from movement within the structure, therefore the entire building required remedial work.
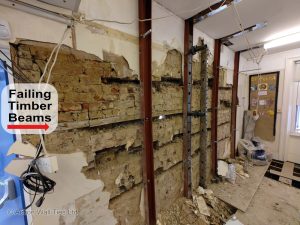
The building appeared to be solid brickwork, however, AWT was prepared for the possibility of decaying timbers within the structure. When the internal plaster was removed, it revealed failing wooden beams that could not support their load.
The Structural Solution
The structural repairs included:
- Brickwork Realignment
- Removal of Failing Timber
- Internal Restraint Posts for Severely Bowed Areas
- Bed Joint Reinforcement Beaming
- Lateral Restraints
- Resin Bonded Ties
- Resin Bonded Stainless Steel Pins
- Brickwork Repairs
AWT’s specialist tools and techniques allowed them to straighten and reinforce the brickwork without visible fixings. The severely bowed wall was reinforced with internal restraint posts that would be hidden when the plasterwork was reinstated.
AWT introduced stainless steel reinforcements deep within the masonry. The formation of continuous beams within the existing masonry redistributes the upper-storey loads and restrains diagonal cracking and bulging tendencies.
AWT stabilised the superstructure of the building and repaired the bowing brickwork in just over 2 weeks. This allowed plenty of time for the internal finishes to be reinstated before the start of the new school year, thus avoiding any disruption to the pupils.
As well as providing an efficient, long-term solution, AWT’s work was also very cost-effective, accounting for less than 25% of the original projected cost.
Action Wall Ties are specialist structural repair contractors with the knowledge and experience required to stabilise period properties with severe brickwork defects, such as superstructure issues or bowing brick walls. AWT work with property owners, structural engineers, project managers, education boards, borough councils, local authorities etc. on large and small projects.
AWT is available across London, Kent, Essex, Surrey, and Sussex. To discuss project details or arrange a survey, please use our contact form, email us, or call us on 01227 721 255.